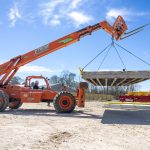
Scale Rentals for All Weighing Needs
April 14, 2025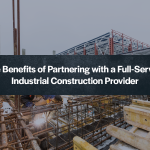
Benefits of an All-in-One Industrial Construction Provider
June 9, 2025Industrial weighing plays a crucial role across multiple industries, from manufacturing and logistics to agriculture and construction. And whether you’re weighing raw materials, monitoring product output or tracking shipments, accuracy is vital. But beyond accuracy, businesses must ensure compliance with industry regulations to avoid costly mistakes.
Regulatory compliance in industrial weighing is not just about ticking boxes, but about maintaining operational efficiency, ensuring safety and protecting your business. Failure to comply with regulations can result in inaccurate measurements, financial penalties and even a damaged reputation. Let’s explore why regulatory compliance is essential and how businesses can stay ahead of the curve.
What is Regulatory Compliance in Industrial Weighing?
Regulatory compliance in industrial weighing means ensuring that all scales and weighing equipment meet legal and industry-specific standards for accuracy, safety and performance. These regulations protect businesses from costly penalties, prevent safety risks and ensure fair trade practices.
Our highest priority is maintaining the strictest safety standards on every project, ensuring the well-being of our team and the security of your operations at all times. We adhere to industry-leading safety and compliance certifications, including:
- Avetta: Ensuring stringent compliance with safety and operational standards.
- ISN RAVS Plus Participant: Demonstrating best-in-class workplace safety and risk management practices.
- SAP Ariba: Partnering with businesses through a trusted, compliant procurement network.
- Alliance & DISA: Meeting high standards for safety, performance, and workforce compliance.
Beyond safety, compliance with industry-specific regulations is important for maintaining accurate and reliable weighing operations. Some of the key regulatory bodies and standards include:
- NIST (National Institute of Standards and Technology): Sets measurement standards in the U.S. to ensure accuracy and fairness in trade.
- ISO (International Organization for Standardization): Provides global standards for weighing equipment and quality management.
- OSHA (Occupational Safety and Health Administration): Regulates workplace safety, including weighing systems used in hazardous environments.
- Local & State Weights and Measures Departments: Ensure businesses meet legal requirements for trade weighing.
Compliance with these regulations guarantees that weighing equipment functions correctly, meets safety standards and operates within legal parameters.
The Consequences of Non-Compliance
Ignoring regulatory compliance for your industrial weighing systems can lead to serious consequences that affect your bottom line, reputation and ability to operate efficiently. Here’s what’s at stake:
1. Legal and Financial Penalties
Non-compliance can result in steep fines and legal action from regulatory agencies. Businesses that use wrong or unapproved scales in trade can face lawsuits, fines and even criminal charges. For example, a company that uses unapproved truck scales to measure freight may face penalties which can lead to financial loss and legal problems.
2. Operational Disruptions and Downtime
If inspectors find your weighing equipment is not in compliance, you may need to halt operations until it’s fixed. This can cause costly downtime and delay production schedules, shipping and overall business efficiency. Unplanned downtime is a costly result of non-compliance. It can cost companies thousands or even millions of dollars in lost productivity.
3. Reputation Damage and Customer Trust Issues
Inaccurate weighing systems can result in incorrect pricing, product inconsistency and loss of customer confidence. If your scales under-weigh or over-weigh products, customers may feel deceived and ultimately leave complaints, negative reviews or damaged business relationships. Non-compliance not only risks regulatory penalties but also damages brand credibility and customer retention.
Key Compliance Factors for Industrial Weighing Systems
1. Calibration and Accuracy Standards
Industrial scales must be routinely calibrated to maintain accuracy and prevent measurement errors. Over time, factors like wear and tear, environmental conditions and frequent use can cause scales to drift out of alignment. Regular certified calibration ensures that your weighing systems meet legal tolerances and industry accuracy requirements.
2. Scale Certification Requirements
Many industries require certified weighing equipment to legally conduct business. Certification ensures that someone tests and approves your scales for compliance with national and industry-specific regulations. At Pro Scales and Construction Services, we offer expert scale certification. This keeps your business compliant and running smoothly.
3. Data Integrity & Record-Keeping
Regulatory agencies often require businesses to maintain records of scale calibration, certification and maintenance. These records serve as proof of compliance in the event of an inspection. Keeping accurate logs and reports will help your business avoid fines and maintain operational integrity.
4. Safety & Workplace Regulations
Beyond measurement accuracy, compliance with workplace safety regulations is critical. Poorly maintained or improperly installed weighing systems can create hazards for workers and lead to injuries, fines and liability issues. Regularly installing and inspecting all scales reduces the risk of workplace accidents and regulatory violations.
Stay Compliant with Industrial Weighing Regulations
Achieving and maintaining compliance requires a proactive approach. Here’s how you can ensure your weighing systems remain up to standard:
- Schedule Regular Calibration and Certification: Work with a trusted provider like Pro Scales and Construction Services. This will help ensure accuracy and meet legal requirements.
- Train Employees on Compliance Standards: Make sure your team understands regulations and follows best practices for using, maintaining and documenting scale performance.
- Conduct Routine Equipment Inspections: Identify and fix issues before they become compliance violations.
- Adhere to a Preventative Maintenance Plan: Prevent breakdowns, extend equipment lifespan and ensure regulatory compliance by following a structured maintenance plan.
By taking these steps, businesses can avoid costly fines, prevent downtime and maintain a reputation for accuracy and reliability.
How Pro Scales and Construction Services Helps You Stay Compliant
At Pro Scales and Construction Services, we specialize in keeping your industrial weighing systems compliant, accurate, and efficient. Our expert team offers:
- Comprehensive Scale Certification: Ensuring compliance with NIST, ISO and local regulatory standards.
- Preventative Maintenance Programs: Designed to minimize downtime and keep scales operating at peak performance.
- 24/7 Emergency Scale Repair: Immediate response to breakdowns to prevent compliance issues and operational disruptions.
- Turnkey Scale Installation: Professional installation that meets all safety and accuracy standards.
We work with businesses across industrial, manufacturing, transportation and commercial sectors to maintain compliance and avoid costly fines.
Regulatory compliance in industrial weighing is not optional—it’s essential for accuracy, safety, legal operation and business success. Failing to comply with regulations can result in hefty fines, legal consequences and damaged business reputation.
Need help staying compliant? Contact Pro Scales and Construction Services today for expert calibration, certification and preventative maintenance solutions. Schedule your compliance check today.